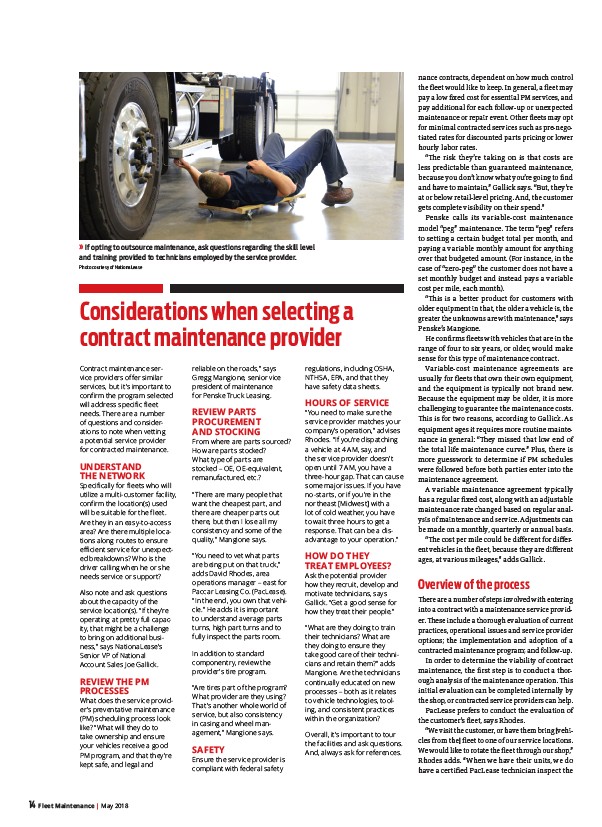
» If opting to outsource maintenance, ask questions regarding the skill level
and training provided to technicians employed by the service provider.
Photo courtesy of NationaLease
14 Fleet Maintenance | May 2018
nance contracts, dependent on how much control
the fl eet would like to keep. In general, a fl eet may
pay a low fi xed cost for essential PM services, and
pay additional for each follow-up or unexpected
maintenance or repair event. Other fl eets may opt
for minimal contracted services such as pre-negotiated
rates for discounted parts pricing or lower
hourly labor rates.
“Th e risk they’re taking on is that costs are
less predictable than guaranteed maintenance,
because you don’t know what you’re going to fi nd
and have to maintain,” Gallick says. “But, they’re
at or below retail-level pricing. And, the customer
gets complete visibility on their spend.”
Penske calls its variable-cost maintenance
model “peg” maintenance. Th e term “peg” refers
to setting a certain budget total per month, and
paying a variable monthly amount for anything
over that budgeted amount. (For instance, in the
case of “zero-peg” the customer does not have a
set monthly budget and instead pays a variable
cost per mile, each month).
“Th is is a better product for customers with
older equipment in that, the older a vehicle is, the
greater the unknowns are with maintenance,” says
Penske’s Mangione.
He confi rms fl eets with vehicles that are in the
range of four to six years, or older, would make
sense for this type of maintenance contract.
Variable-cost maintenance agreements are
usually for fl eets that own their own equipment,
and the equipment is typically not brand new.
Because the equipment may be older, it is more
challenging to guarantee the maintenance costs.
Th is is for two reasons, according to Gallick. As
equipment ages it requires more routine maintenance
in general: “Th ey missed that low end of
the total life maintenance curve.” Plus, there is
more guesswork to determine if PM schedules
were followed before both parties enter into the
maintenance agreement.
A variable maintenance agreement typically
has a regular fi xed cost, along with an adjustable
maintenance rate changed based on regular analysis
of maintenance and service. Adjustments can
be made on a monthly, quarterly or annual basis.
“Th e cost per mile could be diff erent for diff erent
vehicles in the fl eet, because they are diff erent
ages, at various mileages,” adds Gallick.
Overview of the process
Th ere are a number of steps involved with entering
into a contract with a maintenance service provider.
Th ese include a thorough evaluation of current
practices, operational issues and service provider
options; the implementation and adoption of a
contracted maintenance program; and follow-up.
In order to determine the viability of contract
maintenance, the fi rst step is to conduct a thorough
analysis of the maintenance operation. Th is
initial evaluation can be completed internally by
the shop, or contracted service providers can help.
PacLease prefers to conduct the evaluation of
the customer’s fl eet, says Rhodes.
“We visit the customer, or have them bring vehicles
from the fl eet to one of our service locations.
We would like to rotate the fl eet through our shop,”
Rhodes adds. “When we have their units, we do
have a certifi ed PacLease technician inspect the
Considerations when selecting a
contract maintenance provider
Contract maintenance service
providers offer similar
services, but it’s important to
confirm the program selected
will address specific fleet
needs. There are a number
of questions and considerations
to note when vetting
a potential service provider
for contracted maintenance.
UNDERSTAND
THE NETWORK
Specifically for fleets who will
utilize a multi-customer facility,
confirm the location(s) used
will be suitable for the fleet.
Are they in an easy-to-access
area? Are there multiple locations
along routes to ensure
efficient service for unexpected
breakdowns? Who is the
driver calling when he or she
needs service or support?
Also note and ask questions
about the capacity of the
service location(s). “If they’re
operating at pretty full capacity,
that might be a challenge
to bring on additional business,”
says NationaLease’s
Senior VP of National
Account Sales Joe Gallick.
REVIEW THE PM
PROCESSES
What does the service provider’s
preventative maintenance
(PM) scheduling process look
like? “What will they do to
take ownership and ensure
your vehicles receive a good
PM program, and that they’re
kept safe, and legal and
reliable on the roads,” says
Gregg Mangione, senior vice
president of maintenance
for Penske Truck Leasing.
REVIEW PARTS
PROCUREMENT
AND STOCKING
From where are parts sourced?
How are parts stocked?
What type of parts are
stocked – OE, OE-equivalent,
remanufactured, etc.?
“There are many people that
want the cheapest part, and
there are cheaper parts out
there, but then I lose all my
consistency and some of the
quality,” Mangione says.
“You need to vet what parts
are being put on that truck,”
adds David Rhodes, area
operations manager – east for
Paccar Leasing Co. (PacLease).
“In the end, you own that vehicle.”
He adds it is important
to understand average parts
turns, high part turns and to
fully inspect the parts room.
In addition to standard
componentry, review the
provider’s tire program.
“Are tires part of the program?
What provider are they using?
That’s another whole world of
service, but also consistency
in casing and wheel management,”
Mangione says.
SAFETY
Ensure the service provider is
compliant with federal safety
regulations, including OSHA,
NTHSA, EPA, and that they
have safety data sheets.
HOURS OF SERVICE
“You need to make sure the
service provider matches your
company’s operation,” advises
Rhodes. “If you’re dispatching
a vehicle at 4 AM, say, and
the service provider doesn’t
open until 7 AM, you have a
three-hour gap. That can cause
some major issues. If you have
no-starts, or if you’re in the
northeast Midwest with a
lot of cold weather, you have
to wait three hours to get a
response. That can be a disadvantage
to your operation.”
HOW DO THEY
TREAT EMPLOYEES?
Ask the potential provider
how they recruit, develop and
motivate technicians, says
Gallick. “Get a good sense for
how they treat their people.”
“What are they doing to train
their technicians? What are
they doing to ensure they
take good care of their technicians
and retain them?” adds
Mangione. Are the technicians
continually educated on new
processes – both as it relates
to vehicle technologies, tooling,
and consistent practices
within the organization?
Overall, it’s important to tour
the facilities and ask questions.
And, always ask for references.